Presentation:
My thoughts on how the presentation went to today are mainly that I think the presentation went well overall with the exception of our group running out of time in the preparation to get a proper ‘Voice Over’ for the presentational video done.
This was due to the problem, which all the groups faced, of the time it took to render the animation in 3D Studio Max. Mostly the overall average rendering time for all the groups were between 20 -60 hrs, our groups rendering time was 20 hrs even when rendering our animation on 6 separate machines. This limitation caused most of the group’s animations, when presented, to seem a bit segmented instead of running smoothly.
There were several recommendations and alterations suggested to all the groups from both our module leader and the 3 representatives from the ‘Museum of Power’.
The suggestions made to our group were:
• To slow down the rotation of the ‘Griffon Engine’ in our animation so that the viewers would not feel so queasy after watching the video.
• To re-record our ‘Voice Over’ for the video and to edit the content of the script to the ‘Voice Over’ to a less detailed description of the ‘Griffon Engine’ and it’s inner workings to simplified level suitable for younger viewers.
Module Reflection:
For this Module during the past semester I have found the work both interesting and challenging. I have learned several new techniques and modelling styles through following the tutorials during week’s 2 to 5 while constructing the 3D, animated Model of my own head, granted if I had had more time then I would have done a lot more on the 3D Modelling aspects of actually building the head, but out of what I do I feel I learned quite a lot and have extended my knowledge and understanding of the 3D Studio Max Software.
The part about this Module I found most challenging was possibly working under pressure to get select parts of both briefs done in accordance to a set time frame. An example is in trying to do as much as I could on the 3D Head as I could in the limited time I had and to not get left behind everyone else who, in some cases, had actually finished their heads and even partially animated them.
The part of this module which I most enjoyed was being able to work in a group and be part as a team to create a product at the end of the semester. I particularly found the topic we chose quite interesting, Mk 14 Griffon Engine for the Spitfire Fighter plane used in the 1940’s. I found this topic so interesting because it gave me a chance to research the engine and find out about the mechanics behind it and how it was used through the 2nd World War.
In conclusion I feel that I have gained quite a bit of experience from this module through 3D modelling techniques and also historic as well which I didn’t expect. I’m looking forward to next semester with this module to see what we shall be doing next.
Tuesday, 8 December 2009
Sunday, 6 December 2009
Sem.1 Week 11: Voice Over Script
I received an email during mid week of week 10 by a member of the group asking if I could type up a script for a Voice Over which will be included in the presentational Video.
The topics to be covered were:
-Why the MK 14 Griffon Engine was Designed and Developed.
-How the Griffon compares with it's smaller predecessor the Merlin Engine.
-Why is the Griffon, being a V12 engine, better than a Radial engine?
I was able to find a considerable amount of information for comparing the Griffon and Merlin engines and in the Griffon engine'd Design and development but very little on why the V12 Griffon is better than a radial engine.
I produced the script after resaerching about all three engines on the below 3 sites and by asking a local expert about the engines.
Griffon
Merlin
Radial
From this research I was able to produce the below Script:
Person 1:
Hello. This is a virtual representation of an MK 14 Griffon engine.
The ‘Griffon’ engine was originally designed and developed by Rolls-Royce to be interchangeable with its predecessor the ‘Merlin’ engine, and was to be used for low altitude naval aircraft such as the Fairey Firefly. However, during its development, it was suggested that the ‘Griffon’ engine would be adapted to fit in a Spitfire. This suggestion was made by Supermarine’s chief design engineer Joe Smith in 1940.
Later on in the engine’s development however, work on the ‘Griffon’ engine was halted to move focus and concentration to the smaller 27 L ‘Merlin’ which had already surpassed with the early ‘Griffon’ engine design. This was made so, on the order of Lord Beaver Brook, the Minister of Aircraft Production.
The Griffon, when compared with the designs of its earlier predecessors, had several advancements in its design. Physically it was only slightly larger than the Merlin in spite of the Griffon’s larger fuel capacity of 37 litres to the Merlin’s 27. The other main difference was the Griffon’s camshaft and magneto drives were built into the propeller reduction gears at the front of the engine rather than being driven from the back of the camshaft.
This, in turn, allowed the overall length of the engine to be reduced which proved to make the Griffon engine more reliable and efficient, not only by reducing the engine’s length but also due to the idea of fitting the Griffon with an internal oil flow system which contributed to the lubrication of the engine and required less maintenance compared to the Merlin’s external oil lines which required much more maintenance and were prone to leakage.
The topics to be covered were:
-Why the MK 14 Griffon Engine was Designed and Developed.
-How the Griffon compares with it's smaller predecessor the Merlin Engine.
-Why is the Griffon, being a V12 engine, better than a Radial engine?
I was able to find a considerable amount of information for comparing the Griffon and Merlin engines and in the Griffon engine'd Design and development but very little on why the V12 Griffon is better than a radial engine.
I produced the script after resaerching about all three engines on the below 3 sites and by asking a local expert about the engines.
Griffon
Merlin
Radial
From this research I was able to produce the below Script:
Person 1:
Hello. This is a virtual representation of an MK 14 Griffon engine.
The ‘Griffon’ engine was originally designed and developed by Rolls-Royce to be interchangeable with its predecessor the ‘Merlin’ engine, and was to be used for low altitude naval aircraft such as the Fairey Firefly. However, during its development, it was suggested that the ‘Griffon’ engine would be adapted to fit in a Spitfire. This suggestion was made by Supermarine’s chief design engineer Joe Smith in 1940.
Later on in the engine’s development however, work on the ‘Griffon’ engine was halted to move focus and concentration to the smaller 27 L ‘Merlin’ which had already surpassed with the early ‘Griffon’ engine design. This was made so, on the order of Lord Beaver Brook, the Minister of Aircraft Production.
The Griffon, when compared with the designs of its earlier predecessors, had several advancements in its design. Physically it was only slightly larger than the Merlin in spite of the Griffon’s larger fuel capacity of 37 litres to the Merlin’s 27. The other main difference was the Griffon’s camshaft and magneto drives were built into the propeller reduction gears at the front of the engine rather than being driven from the back of the camshaft.
This, in turn, allowed the overall length of the engine to be reduced which proved to make the Griffon engine more reliable and efficient, not only by reducing the engine’s length but also due to the idea of fitting the Griffon with an internal oil flow system which contributed to the lubrication of the engine and required less maintenance compared to the Merlin’s external oil lines which required much more maintenance and were prone to leakage.
Friday, 27 November 2009
Sem. 1 Week 10: Week 10 Lecture
During this lecture, the group discussed two things.
The first being, the animation of the entire project, there have been concerns that we will not be able to construct the animation we originally planned to implement and instead will be altering the original animation idea. so, instead of having the plane take off, fly around and into a close up to reveal the inner workings of the engine. It will show the plane in flight already, a brief history of the plane and a cut scene of the inner workings of the 'Griffon engine'.
The second thing which was discussed was the script for facts about the Spitfire and its history and a script for a voice over detailing the inner workings of Spitfire Engine.
The first being, the animation of the entire project, there have been concerns that we will not be able to construct the animation we originally planned to implement and instead will be altering the original animation idea. so, instead of having the plane take off, fly around and into a close up to reveal the inner workings of the engine. It will show the plane in flight already, a brief history of the plane and a cut scene of the inner workings of the 'Griffon engine'.
The second thing which was discussed was the script for facts about the Spitfire and its history and a script for a voice over detailing the inner workings of Spitfire Engine.
Tuesday, 24 November 2009
Sem. 1 Week 9-10: Material Maps
I have now begun work on creating the Material Maps for the hangar and adding them to the hangar model.
First, opening Photoshop and opening both the ‘Rivet’ and ‘Stainless Steel’ images. From those images I can create the stainless roof for the Hangar.

I proceeded from here by increasing the canvas size by four times the current size to create more space to duplicate the stainless steel plates to give a layered effect for the roof.
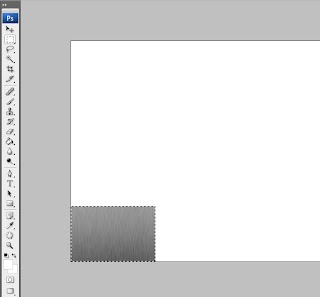
Leaving that for the moment, I set about turning my attention on editing the ‘Rivet’ image by using the ‘Quick Mask Mode’ in Photoshop.
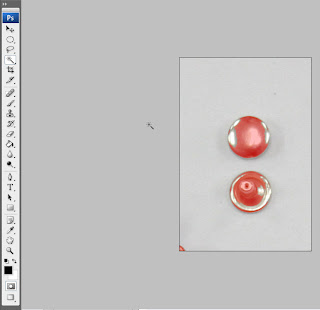
This creates the finished result below.
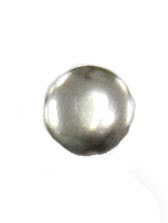
Taking the above image of the ‘Rivet’ I added it onto the ‘Stainless Steel’ image on a separate layer to show a riveted plate. I did this a total of 4 times in each corner.
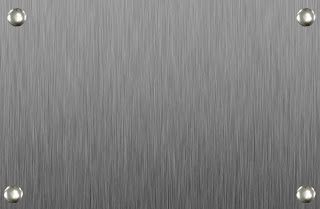
The final step was selecting the riveted, stainless steel image and duplicating it on several layers to fill the remaining canvas space.
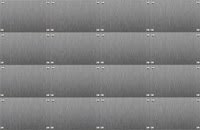
Now that the Map has been finished in Photoshop, I can move on to adding both maps to the 3D Model on ‘Studio Max’.
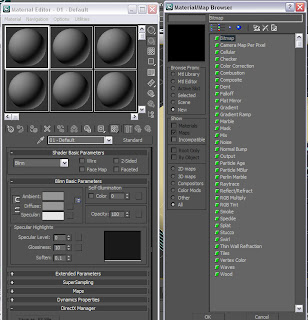.jpg)
Opening up ‘Hangar example 1.3dsMax scene’ file and opening ‘Material Editor, I selected ‘Diffuse colour’ and selected ‘bitmap’, opening ‘stainless_steel_3.jpg’ and added it to the roof of the hangar model.
After adding the map initially, I found that the image file was much too big because it was showing up as a black on the material editor. I attempted to correct this by changing the size of the image in Photoshop, although it appeared I needed to resize the image several times by tweaking the ‘Image Size’ tool in Photoshop before it would show up on the material editor.
I did the same with ‘CONCRETE_014.jpg’ file and dragged the map from the ‘Material Editor’ to the wall of the hangar.
.jpg)
I showed the progress I made on the model thus far to the lecturer and it was suggested that I add some texture to give the model a bit more depth. I took her suggestion on board and first added a ‘Bump’ Texture to the wall to see how it would look.
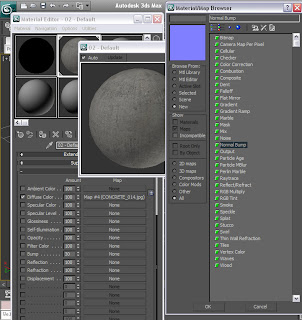.jpg)
I wasn’t satisfied with the outcome, mainly because it hardly showed at all on the model so I decided to go with a dent texture instead to see if it would give the appropriate effect.
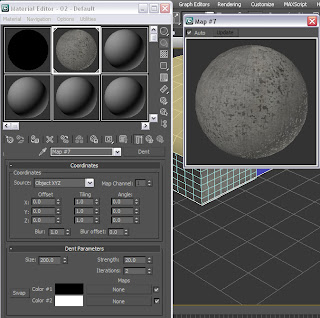.jpg)
I was pleased with the result as the ‘Dent’ texture did indeed give the concrete wall a more realistic feel.
Now that I am pleased with model textures I decided it was time to group all the model components together so that there would be less to export later.
Before I grouped the hangar components, I decided to first duplicate the hangar by first selecting all the components of the model then, using the ‘Clone’ tool, dragged the copied hangar alongside the first to give a better feel of an airport with multiple aircraft hangars.
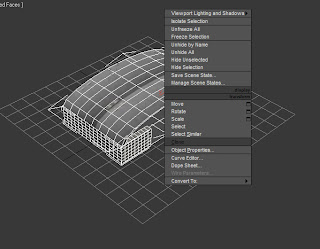
After cloning the hangar I did a render of the scene so far and this is the result.
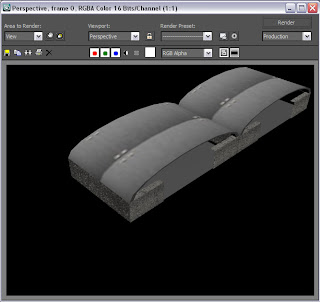
After having rendered the scene and am pleased with the result I clicked on the ‘Group’ icon on the main toolbar in ‘Studio Max’ and named the group ‘Group1’.
First, opening Photoshop and opening both the ‘Rivet’ and ‘Stainless Steel’ images. From those images I can create the stainless roof for the Hangar.

I proceeded from here by increasing the canvas size by four times the current size to create more space to duplicate the stainless steel plates to give a layered effect for the roof.
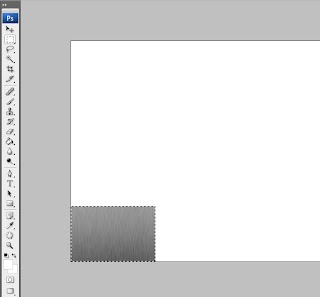
Leaving that for the moment, I set about turning my attention on editing the ‘Rivet’ image by using the ‘Quick Mask Mode’ in Photoshop.
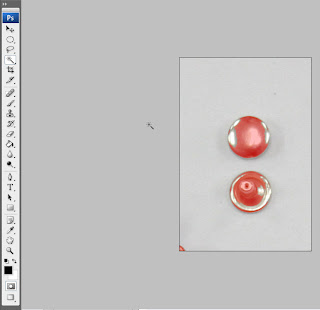
This creates the finished result below.
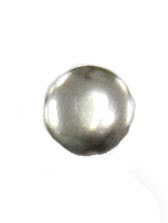
Taking the above image of the ‘Rivet’ I added it onto the ‘Stainless Steel’ image on a separate layer to show a riveted plate. I did this a total of 4 times in each corner.
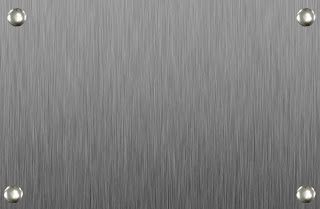
The final step was selecting the riveted, stainless steel image and duplicating it on several layers to fill the remaining canvas space.
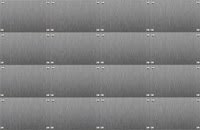
Now that the Map has been finished in Photoshop, I can move on to adding both maps to the 3D Model on ‘Studio Max’.
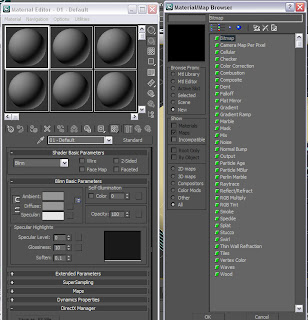.jpg)
Opening up ‘Hangar example 1.3dsMax scene’ file and opening ‘Material Editor, I selected ‘Diffuse colour’ and selected ‘bitmap’, opening ‘stainless_steel_3.jpg’ and added it to the roof of the hangar model.
After adding the map initially, I found that the image file was much too big because it was showing up as a black on the material editor. I attempted to correct this by changing the size of the image in Photoshop, although it appeared I needed to resize the image several times by tweaking the ‘Image Size’ tool in Photoshop before it would show up on the material editor.
I did the same with ‘CONCRETE_014.jpg’ file and dragged the map from the ‘Material Editor’ to the wall of the hangar.
.jpg)
I showed the progress I made on the model thus far to the lecturer and it was suggested that I add some texture to give the model a bit more depth. I took her suggestion on board and first added a ‘Bump’ Texture to the wall to see how it would look.
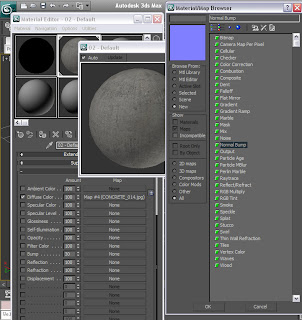.jpg)
I wasn’t satisfied with the outcome, mainly because it hardly showed at all on the model so I decided to go with a dent texture instead to see if it would give the appropriate effect.
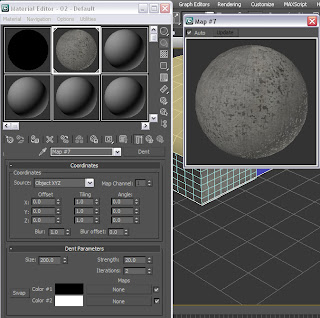.jpg)
I was pleased with the result as the ‘Dent’ texture did indeed give the concrete wall a more realistic feel.
Now that I am pleased with model textures I decided it was time to group all the model components together so that there would be less to export later.
Before I grouped the hangar components, I decided to first duplicate the hangar by first selecting all the components of the model then, using the ‘Clone’ tool, dragged the copied hangar alongside the first to give a better feel of an airport with multiple aircraft hangars.
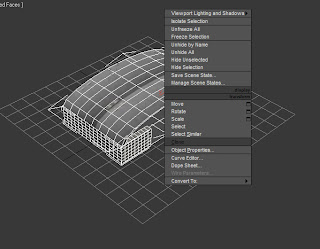
After cloning the hangar I did a render of the scene so far and this is the result.
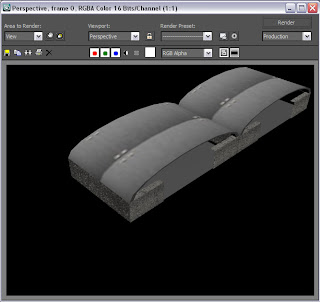
After having rendered the scene and am pleased with the result I clicked on the ‘Group’ icon on the main toolbar in ‘Studio Max’ and named the group ‘Group1’.
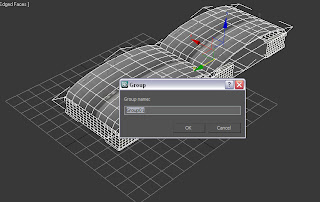
Friday, 13 November 2009
Sem. 1 Week 8: Start of Designing Animation
This lecture, the rest of the group and I discussed how best to animate the virtual environment, first compiling all of our 3D Modelling pieces and importing them all into one document to then be animated later in the session.
I, regrettably, was unable to contribute my 3D Model of an aircraft hangar due to my 3D Studio Max licence expiring during the previous week. However, I recently applied for and received a new licence with Studio Max software and will be able to proceed with my portion of the modelling.
For this session I began looking for preference images which I will, later, be able to edit to make some material maps to make the 3D Model appear more realistic.
Below are some of the preference pics I will be using:
Stainless Steel:
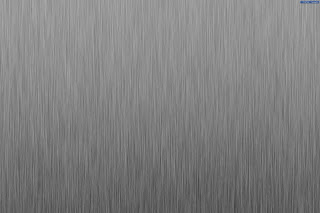
This will possibly be used for the roof and will have a panelled effect. This will include rivets or nails being put on the panels to show how the roof fits together. I will be making these modifications in Photoshop.
Concrete:
(Note: image below is an example.)
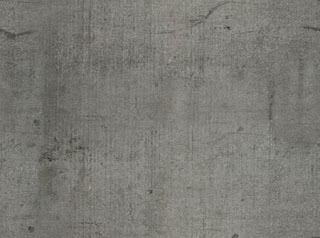
It was suggested by the lecturer that the best way to get an idea of what a concrete wall would look like is to actually take a photo of the real thing and then edit it in Photoshop or, in Studio Max, adding a ‘Bump’ texture to it to represent the texture realistically.
Ridged Steel:
I may need to do the same for the ‘Ridged Steel’ as I am going to do with the concrete and take a photo of it and create a material map for it on Photoshop. I intend for this to be used as the upper half for the outside walls of the hangar.
Metal Rivet
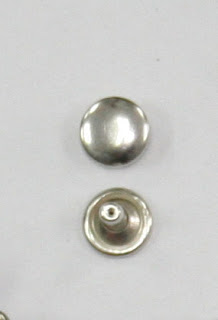
These will be added to the roof material to better show that panels are layered and fastened together to give the illusion of a solid structure.
The above images were found from these Websites:
Steel
Concrete
Metal Rivet
I, regrettably, was unable to contribute my 3D Model of an aircraft hangar due to my 3D Studio Max licence expiring during the previous week. However, I recently applied for and received a new licence with Studio Max software and will be able to proceed with my portion of the modelling.
For this session I began looking for preference images which I will, later, be able to edit to make some material maps to make the 3D Model appear more realistic.
Below are some of the preference pics I will be using:
Stainless Steel:
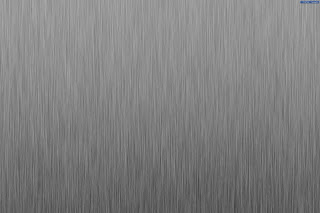
This will possibly be used for the roof and will have a panelled effect. This will include rivets or nails being put on the panels to show how the roof fits together. I will be making these modifications in Photoshop.
Concrete:
(Note: image below is an example.)
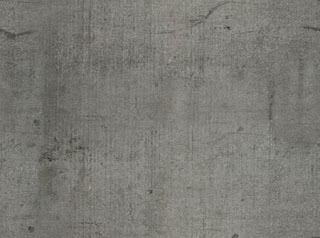
It was suggested by the lecturer that the best way to get an idea of what a concrete wall would look like is to actually take a photo of the real thing and then edit it in Photoshop or, in Studio Max, adding a ‘Bump’ texture to it to represent the texture realistically.
Ridged Steel:
I may need to do the same for the ‘Ridged Steel’ as I am going to do with the concrete and take a photo of it and create a material map for it on Photoshop. I intend for this to be used as the upper half for the outside walls of the hangar.
Metal Rivet
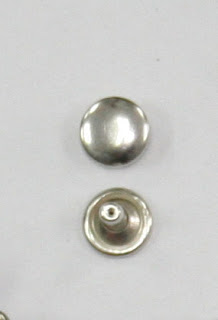
These will be added to the roof material to better show that panels are layered and fastened together to give the illusion of a solid structure.
The above images were found from these Websites:
Steel
Concrete
Metal Rivet
Friday, 6 November 2009
Sem.1 Week 7: Hanger Idea 1 contd.
To start off the modelling process of the Hangar, I first opened up a new Studio Max file and created a ‘Tube’ named ‘tube1’, this will become the roof of the hangar(s). The tube dimensions are: H=8 seg, C=1 seg and Sides=18.
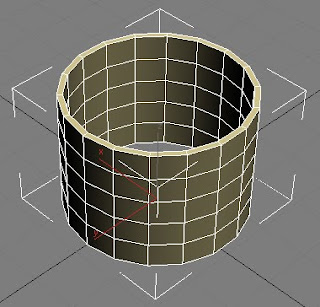
Next, I added an ‘Edit Poly’ modifier to the tube, rotated the tube so that it’s lying on its side with half its mass above and below stage grid and then halved the tube to make a 9 sided semi circular tube. I did this via changing the ‘edit poly’ modifier to ‘Vertex’.
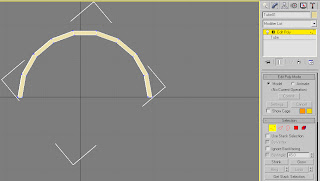
Now that I have the basic shape of the hangar roof I went about reshaping the half tube to better represent the roof in the hangar design shown above. It was suggested to me by my Learning Support Advisor (LSA) that I use the ‘Uniform Scale’ tool, on the main tool bar, to stretch and compress to scale the half tube rather than go use the scenic route and halve the tube again, reshape it one vertex at a time and then duplicate it to get the final result. I personally found the stretch and compress method much easier and less time consuming.
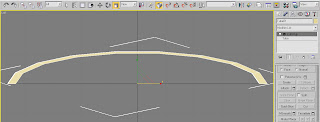
Below is the above image in the perspective view and shows that it has been stretched over all 3 dimensions.
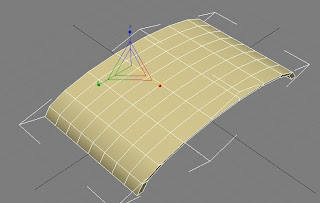
Now that the shape of the roof is done, I moved onto the hangar walls and opening for the doors. I started this by first creating a ‘Box’ called ‘Box1’, and changed the segment dimensions to L=6 seg, W=15 seg and H=33 seg (Shown below).
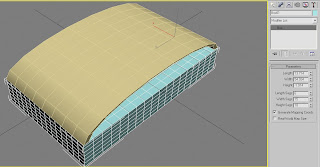
The step I undertook was hollowing out ‘Box1’ in order to form the walls and doors around the outside. I did this by again adding an ‘Edit Poly’ modifier and changing it to ‘Vertex’ and then deleting the inner segments by selecting all the vertex dots, while in ‘top view’ and clicking delete to leave a 1 segment deep wall around the outside.
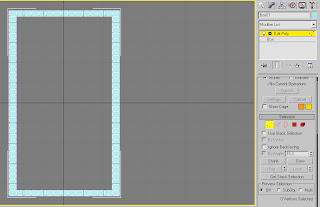
After having created the walls the next step was to make a whole for the plane to go through, this will be the hangar door (Shown in the below Screen Dump).
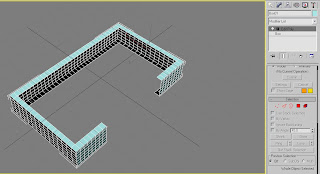
At this stage I discovered a problem with the number of Segments for the height of the box. It appeared that I needed an extra segment on the height of the box for the doors to open and close effectively.
After I tended to this problem, I then started on the doors by creating two planes, rotating them sideways and placing them against the front walls.
Due to new information regarding the animation section which will be done next week, I will not need to create doors for the hanger seeing as the plane won’t be coming out of the hangars.
This said, I can now proceed onto the next step of creating a flat plain for the Hangar floor and begin applying maps and textures to the hangar roof, walls and floor (of which I will begin during next week’s lecture).
Note: Next week the rest of the group will be compiling their 3D models of their allocated tasks and combining them to begin the animation.
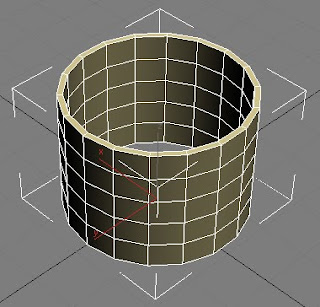
Next, I added an ‘Edit Poly’ modifier to the tube, rotated the tube so that it’s lying on its side with half its mass above and below stage grid and then halved the tube to make a 9 sided semi circular tube. I did this via changing the ‘edit poly’ modifier to ‘Vertex’.
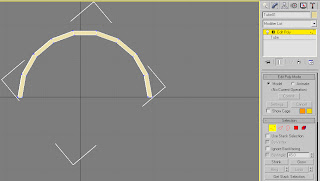
Now that I have the basic shape of the hangar roof I went about reshaping the half tube to better represent the roof in the hangar design shown above. It was suggested to me by my Learning Support Advisor (LSA) that I use the ‘Uniform Scale’ tool, on the main tool bar, to stretch and compress to scale the half tube rather than go use the scenic route and halve the tube again, reshape it one vertex at a time and then duplicate it to get the final result. I personally found the stretch and compress method much easier and less time consuming.
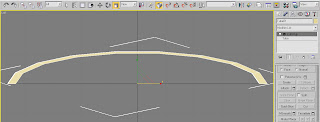
Below is the above image in the perspective view and shows that it has been stretched over all 3 dimensions.
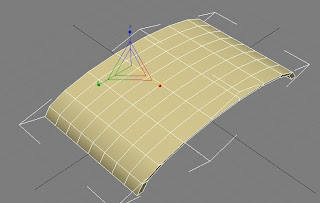
Now that the shape of the roof is done, I moved onto the hangar walls and opening for the doors. I started this by first creating a ‘Box’ called ‘Box1’, and changed the segment dimensions to L=6 seg, W=15 seg and H=33 seg (Shown below).
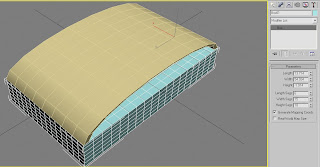
The step I undertook was hollowing out ‘Box1’ in order to form the walls and doors around the outside. I did this by again adding an ‘Edit Poly’ modifier and changing it to ‘Vertex’ and then deleting the inner segments by selecting all the vertex dots, while in ‘top view’ and clicking delete to leave a 1 segment deep wall around the outside.
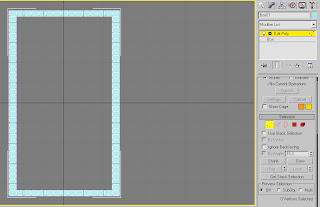
After having created the walls the next step was to make a whole for the plane to go through, this will be the hangar door (Shown in the below Screen Dump).
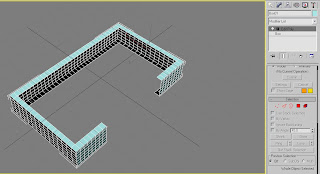
At this stage I discovered a problem with the number of Segments for the height of the box. It appeared that I needed an extra segment on the height of the box for the doors to open and close effectively.
After I tended to this problem, I then started on the doors by creating two planes, rotating them sideways and placing them against the front walls.
Due to new information regarding the animation section which will be done next week, I will not need to create doors for the hanger seeing as the plane won’t be coming out of the hangars.
This said, I can now proceed onto the next step of creating a flat plain for the Hangar floor and begin applying maps and textures to the hangar roof, walls and floor (of which I will begin during next week’s lecture).
Note: Next week the rest of the group will be compiling their 3D models of their allocated tasks and combining them to begin the animation.
Thursday, 5 November 2009
Sem.1 Week 7: Hanger Idea 1
I began work on creating a design Idea on how a Spitfire Hanger would have looked like. Below is a design which I am going to be using as a design base for the hangers I plan to implement in Studio Max.
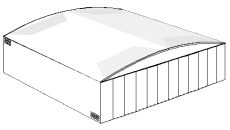
I will want to discuss with the rest of the group next lecture on what Hanger Design I should implement and which would best fit with the period of the airplane the group will be producing.
I will also be printing out a handout, listing the possible hanger design options which I saved from the below website.
www.aircraft-hangars.com
(Note: I also got the above image from the above website.)
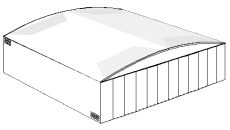
I will want to discuss with the rest of the group next lecture on what Hanger Design I should implement and which would best fit with the period of the airplane the group will be producing.
I will also be printing out a handout, listing the possible hanger design options which I saved from the below website.
www.aircraft-hangars.com
(Note: I also got the above image from the above website.)
Subscribe to:
Posts (Atom)